La temperatura de trabajo en las válvulas es muy elevada, sobretodo en la de escape que llega a alcanzar entre 800° a 1 050°C, por eso están diseñadas para soportar estas duras condiciones de trabajo y a la vez deben ser ligeras para poder cambiar su estado de reposo o movimiento con facilidad. Las válvulas deben tener sus dimensiones estudiadas y apropiadas pues tienen que estar adecuadas a las necesidades requeridas para el llenado (tiempo de admisión) y evacuado (tiempo de escape) de gases durante el funcionamiento del motor.
- CARACTERÍSTICAS CONSTRUCTIVAS DE LAS VÁLVULAS DIÁMETRO DE LA CABEZA DE VÁLVULA
ADMISIÓN:
El mayor diámetro de la cabeza de válvula favorece el llenado a los cilindros de aire procedente de la atmósfera con una velocidad de entrada de 50 a 80 m/s aproximadamente la cual depende del tipo de motor, del diseño y de la velocidad de desplazamiento del émbolo. Para motores con velocidad del émbolo de hasta 6 m/s el diámetro de la cabeza de válvula está comprendido entre 0,3 y 0,35 veces el diámetro del cilindro, pero para motores con velocidad del émbolo superior a 6 m/s, el diámetro de la cabeza de válvula está comprendido entre 0,35 y 0,40 veces el diámetro del cilindro. La válvula de admisión sufre en menor cuantía los efectos de temperatura en la cámara de combustión debido a su constante refrigeración al estar en contacto directo con el aire procedente de la atmósfera y que ingresa al cilindro.
ESCAPE:
Las dimensiones de la cabeza influyen directamente sobre la temperatura de trabajo en las válvulas, ya que a mayor superficie, el calor que incide sobre ella es mayor y por tanto existe una elevada acumulación térmica en esta zona. Debido a esto las válvulas de escape se construyen con tendencia al menor diámetro posible, pero dentro de las exigencias que permitan que los gases quemados tengan una evacuación rápida del cilindro sin crear contrapresiones a la salida de los mismos. La velocidad que en promedio alcanzan los gases quemados es de 70 a 100 m/s.
- ÁNGULO DE LA CARA BISELADA.
ADMISIÓN:
Los fabricantes de motores diésel con Cámara de Inyección Directa diseñan a esta válvula con un ángulo en la cara biselada de 30°, lo cual favorece a la velocidad de turbulencia de aire y al llenado de los cilindros, factores importantes que hacen más eficiente el proceso químico de la combustión. En motores diésel con Cámara de Inyección Indirecta los fabricantes normalmente diseñan a esta válvula con un ángulo de 45°en la cara biselada.

Fig. N° 12. Válvula de admisión
ESCAPE:
Los fabricantes de motores diésel han generalizado el diseño de la válvula de escape, dándole a la cara biselada un ángulo de 45°, lo cual ofrece menor resistencia al paso de los gases, permite un mejor cierre de la cámara de combustión. La válvula adquiere mayor resistencia a la deformación ya que necesita de una estructura más robusta, pues su temperatura de trabajo es muy elevada, llegando a alcanzar entre 800° y 1050°C aproximadamente durante el funcionamiento del motor a plena carga.

Fig. N° 13. Válvula de escape
- TOLERANCIA EN ENTRE EL VÁSTAGO Y SU GUÍA
Las dimensiones del vástago con su guía deben permitir un ajuste muy preciso, con el fin de garantizar un deslizamiento suave y a la vez evitar:
- Que los gases quemados entren al circuito de ventilación del cárter por una excesiva holgura entre el vástago de la válvula de escape y su guía, ya que se origina en este espacio desgastado, una compresión de gases quemados por la fuerza de empuje que sufren estos, debido a la velocidad de salida que adquieren en el orificio de escape; de esta forma los gases quemados llegan a deteriorar las propiedades y características del aceite de engrase del motor.
En las válvulas de admisión suele darse un ajuste de montaje que corresponde a una holgura de 0,002" a 0,003" (0,051 a 0,076mm). Debido a su mayor dilatación térmica en la válvulas de escape suele darse un ajuste de montaje que corresponde a una holgura de 0,003" a 0,004" (0,076 a 0,10mm).
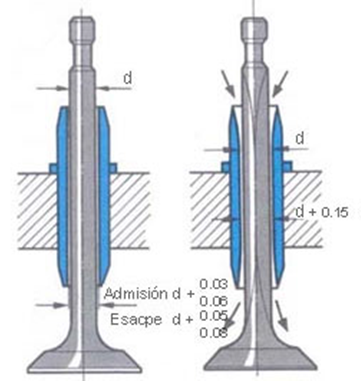
Fig. N° 14.válvulas de admisión y escape
- MATERIALES EMPLEADOS EN SUFABRICACIÓN
ADMISIÓN:
En las válvulas de admisión se emplean aceros de menor calidad que en las de escape debido a las condiciones de trabajo menos rigurosas; generalmente se trata de aceros al carbono con pequeñas proporciones de cromo silicio y níquel, estos aceros alcanzan una resistencia a la tracción de 55 Kg-f/mm2. A la cara biselada de la válvula de admisión en algunos casos se le da el mismo tratamiento que en la de escape, recargándole en esta zona con estelita (aleación de cromo- acero- tungsteno-carbón) con lo cual adquiere mayor resistencia al desgaste y a la corrosión.
ESCAPE:
Para las válvulas de escape, debido a las elevadas temperaturas de trabajo que tiene que soportar, se emplean aceros austeníticos al cromo- níquel, al tungsteno-silicio o aceros al cobalto-molibdeno-tungsteno; todos ellos son muy resistentes al calor y a la corrosión, con una elevada resistencia mecánica a la tracción del orden de los 120 Kg-f/mm2 y a temperaturas de 1 150°C. Este tipo de material a pesar de sus buenas características térmicas y mecánicas, se desgasta con facilidad, para evitar este inconveniente se somete la zona del vástago a un tratamiento de nitruración.
- VÁLVULAS ESPECIALES
VÁLVULA CON DEFLECTOR:
Se emplea generalmente como válvula de admisión en motores diésel con Cámara de Inyección Directa para dar la orientación adecuada al ingreso de aire y favorecer la turbulencia en el interior del cilindro haciendo más eficiente el proceso químico de la combustión.

Fig. N° 15. Válvula con deflector
VÁLVULA CON RELLENO DE SODIO:
En motores de gran potencia las válvulas están sometidas a elevadas temperaturas, se emplean para el escape válvulas refrigeradas interiormente con sodio metálico el cual reúne las siguientes características:
- Bajo peso específico.
- Calor específico elevado.
- Bajo punto de fusión.
- Elevado punto de ebullición.

Fig. N° 16. Válvula con relleno de sodio
Su vástago se fabrica hueco y se rellena con sodio de forma que durante su funcionamiento el sodio se licúa debido a su bajo punto de fusión y absorbe por su elevado calor específico, el calor que la cabeza transmite al vástago. Su elevado punto de ebullición hace que no llegue a dilatarse excesivamente por las temperaturas de trabajo a que está sometida la válvula.
VÁLVULAS BIMETÁLICAS:
Se le denomina así porque la cabeza de la válvula está diseñada con materiales que soportan elevadas presiones y temperaturas, pero el vástago con materiales que son resistentes al desgaste y a la corrosión.
- LUZ - HOLGURA DE CALIBRACIÓN.
Durante el funcionamiento del sistema de distribución, se produce por efectos de temperatura, una serie de dilataciones conjugadas en válvulas y elementos de empuje que debe compensarse con una pequeña holgura entre el balancín y el pie de la válvula. El correcto reglaje de esta holgura es lo que se conoce como "Reglaje de Taques" o "Calibración de Válvulas"; esta operación es de suma importancia para el buen funcionamiento del sistema, ya que si se deja una holgura insuficiente, al producirse la dilatación la válvula podría quedar abierta, en cuyo caso existirían fugas durante la compresión.
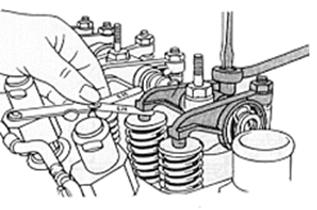
Por el contrario, si la holgura es excesiva, el mayor recorrido del balancín hace que la válvula tarde más en abrirse y que se cierre antes del momento preciso, lo cual distorsiona los ángulos de apertura y cierre de válvulas previstos en el diagrama real práctico de distribución. La holgura correspondiente a cada tipo determinada por el fabricante del motor, la cual ha sido fijada previamente en la fase experimental del mismo, para que cumpla exactamente la función de compensar los defectos de llenado y evacuado de gases, sin distorsionar el correcto funcionamiento del sistema.
Esta luz-holgura de calibración suele variar para cada tipo de motor, sistema de distribución y para cada válvula; y normalmente está en un rango de 0,008" a 0,014" (0,20 a 0,35 mm) para motores diésel livianos y medianos, pero para motores diésel pesados el rango normalmente esta entre 0,012" a 0,020" (0,30 a 0,50 mm), siendo generalmente mayor en la de escape por estar sometida a elevadas temperaturas. Las válvulas se fabrican generalmente de una sola pieza, partiendo de una varilla cilíndrica calibrada y se obtiene la forma adecuada de la cabeza por procedimientos de extrusión o recalcado del material en caliente. El calentamiento de la varilla hasta la temperatura adecuada se consigue por inducción eléctrica.
- COMPROBACIÓN DEL ESTADO DE LAS VÁLVULAS
Las válvulas en continuo desplazamiento de apertura y cierre, están sometidas a continuos desgastes y deformaciones producidos por los rozamientos y los choques. La elevada temperatura a que están expuestas contribuye a ello. Los desgastes y deformaciones que se producen en las válvulas y que se deben comprobar son los siguientes:
- Desgaste en la cabeza y asiento de válvula.
- Deformaciones, sobre todo en la válvula de escape, debido a la temperatura de los gases quemados y a la influencia de los agentes químicos de la combustión.
- Deformación en el vástago y desgaste por rozamiento en su guía.
Antes de proceder a la comprobación de las válvulas, debe marcarse su posición de referencia según se van desmontando, con objeto de poder colocarlas en el mismo lugar que tenían en la culata, ya que cada válvula ajusta en su respectivo asiento.
Deben limpiarse cuidadosamente las cabezas, asientos y guías, con el fin de eliminar la carbonilla depositada en esas zonas. Esta operación se realiza en la electro esmeriladora, con un disco de cerdas metálicas o con una escobilla metálica y luego se desprenden las partículas adheridas con aire a presión.
Se comprueba que las superficies de asiento en la válvula y en la pieza postiza están perfectamente lisas y pulidas, sin señales de rayaduras o erosiones. Si no aparecen señales de erosión, solo se realiza un ejercicio de asentamiento sobre su asiento con pasta abrasiva. Hay que comprobar que el vástago esta torcido o la cabeza se ha deformado. Para ello se coloca la válvula entre puntos y con un reloj comparador, se mide la alineación del vástago, así como el descentrado de la cabeza. De existir la menor desviación de la aguja en cualquiera de estas operaciones debe sustituirse la válvula. El juego de montaje entre el vástago y su guía es de 0,002" (0,05 mm) como promedio, para la válvula de admisión, y de 0,003" (0,07 mm) para la válvula de escape, aún se admite una holgura máxima de 0,005" (0,12 mm). En caso de ser mayor esta holgura, debe cambiarse la guía. La operación del rectificado consiste en repasar las superficies de asiento de la cabeza hasta que queden perfectamente lisas y a la medida deseada, En los asientos de válvula, esta operación se realiza por medio de una fresa sujeta a un mango y guiada a mano o con máquinas portátiles apropiadas.
La fresa de avellanar debe tener un corte a 45° o 30°, según sea el caso, ya que estas por lo general son los ángulos de inclinación de la superficie de apoyo del asiento.
Además de la superficie de apoyo propiamente dicho se mecaniza un cono de entrada con una fresa de 20° y luego otro de salida con una fresa de 75°, que además de dejar la superficie a la medida dejan también el asiento a la altura adecuada. Después del fresado, si es necesario, se rectifica la válvula en máquinas especiales destinadas a tal fin, en esta operación se debe tener en cuenta que la cabeza de la n válvula no se debilite. Por este motivo, el rectificado de la válvula sólo debe hacerse cuando la erosión es poco pronunciada, pues, de ser excesiva debe cambiarse la válvula. Después del rectificado se procede al esmerilado, consiste en frotar la cabeza de la válvula contra su asiento interponiendo una capa de pasta esmeril.
Esta operación proporciona un cierre hermético de la válvula en su asiento y se realiza aplicando una ventosa sobre la cabeza de la válvula haciéndola girar en ambos sentidos. La altura a que queda la válvula una vez rectificada se puede verificar con respecto a la culata por medio de un calibre de profundidades o un reloj comparador. El alabeo se puede comprobar por medio de un reloj comparador y por último para comprobar el cierre el cierre hermético de la válvula contra su asiento, se utiliza un dispositivo especial en forma de campana de aire que se coloca sobre la cámara de combustión haciendo un cierre hermético por contacto. Se inyecta aire a presión en el interior de la campana, la desviación de la aguja en el manómetro indica si hay fugas a través de las válvulas o por el contrario, si la aguja se mantiene en la presión introducida es que el cierre de las válvulas es hermético.
- ASIENTOS DE VÁLVULAS
Son piezas postizas colocadas a presión sobre la culata y las cuales asientan las válvulas para lograr el cierre hermético de la cámara de combustión. Estas piezas se montan por que el material de la culata es excesivamente blando respecto al de la válvula y no puede soportar el continuo golpeteo a que está sometido el asiento durante su funcionamiento. El material empleado en la fabricación de estas piezas postizas es la fundición centrifugada y nitrurada, aleada con cromo-níquel para obtener una elevada dureza y resistencia al desgaste y corrosión.

Fig. N° 18. Piezas postizas de válvulas
El montaje de los asientos se efectúa a presión por medio de un ajuste térmico, que consiste en calentar la zona de la culata donde va situada la pieza postiza para que se dilate. La pieza a ensamblar se mantiene en un baño de hielo seco para su contracción.

Fig. N° 19. Fresado de válvulas
Una vez colocados los asientos en su alojamiento, el calor de la culata se transmite a las piezas postizas, de forma que, al contraerse la culata y dilatarse las piezas, estas queda perfectamente ajustado a presión. La operación de rectificado consiste en repasar las superficies de asiento de la cabeza hasta que queden perfectamente lisas y a la medida deseada. En los asientos de válvula, esta operación se realiza por medio de una fresa (herramienta de corte circular - cónico) sujeta a un mango y guiada a mano o con máquinas portátiles especiales, la fresa de avellanar debe tener un corte a 45°, ya que ésta es la inclinación de la superficie de asiento.

Fig. N° 20. Fresado de válvulas con ángulos
Además de la superficie de asiento propiamente dicha se mecaniza un cono de entrada con una fresa de 20° y luego otro de salida con una fresa de 75°, que además de dejar la superficie a medida, dejan también el asiento a la altura adecuada. Después del fresado, si es necesario, se rectifica la válvula en máquinas especiales destinadas a tal fin. En esta operación se debe tener en cuenta que la cabeza de la válvula no se debilite, por este motivo, el rectificado de la válvula sólo debe hacerse cuando la erosión es poco pronunciada, pues de ser excesiva, debe cambiarse la válvula.

Fig. N° 21. Rectificado de válvulas
Después del fresado se procede al esmerilado, que consiste en frotar la cabeza de la válvula contra su asiento, interponiendo una capa de pasta abrasiva, esta operación proporciona un cierre hermético sobre la cabeza de la válvula, haciendo la girar en ambos lados.

Fig. N° 21. Asentado de las válvulas
- GUÍAS DE VÁLVULAS.
Las guías de válvulas al igual que los asientos de válvulas son piezas postizas, su forma de casquillos cilíndricos se insertan a presión en la culata siguiendo el mismo proceso indicado anteriormente para los asientos de válvulas. Su misión es de servir de guía al vástago de la válvula durante su desplazamiento, para evitar el desgaste de la culata y transmitir el calor de la válvula al circuito de refrigeración. El material empleado en la fabricación de guías de válvulas es el "NILRESIST", aleación parecida a la de los asientos de piezas postizas (fundición gris al cromo-vanadio) que ofrece además gran resistencia a la fricción, buena conductibilidad al calor, propiedades auto lubricantes, para compensar el escaso flujo de aceite de engrase. Las dimensiones de estas guías deben permitir un ajuste muy preciso con el vástago de la válvula, con el fin de garantizar un deslizamiento suave y a la vez, evitar fugas de gases o entradas indebidas del aceite de engrase a través de una excesiva holgura.

Fig. N° 22. Guías de las válvulas
En las válvulas de admisión suele darse un ajuste de montaje que corresponde a una holgura máxima de 0,002" a 0,003" (0,05 a 0,07 mm) y en válvulas de escape debido a su mayor dilatación, suele darse una holgura de 0,003" a 0,004" (0,07 a 0,10 mm), ambas piezas exigen una calidad superficial elevada.
- MUELLES DE VÁLVULA
Estos elementos tienen la misión de mantener firmemente asentada la válvula contra su alojamiento de la cámara de combustión, impidiendo que ésta se mueva por efecto de la de presión originada en el cilindro durante la admisión. Los muelles están constantemente sometido a esfuerzos alternativos para abrir y cerrar las válvulas. Debido a su elasticidad, se produce una serie de movimientos vibratorios que se transmiten a las válvulas y elementos de mando y ocasionan ciertos rebotes que perjudican el buen funcionamiento del sistema. Por esta razón los resortes empleados han de tener una elasticidad adecuada y han de estar dispuestos de tal forma que, durante su funcionamiento, se compensen las oscilaciones citadas.

Fig. N° 23. Resortes de las válvulas
El sistema empleado para evitar estos efectos oscilantes consiste en fabricar los muelles con carga elástica de tensión gradual, reduciendo el paso de las espiras próximas a su asiento en la culata e incrementando progresivamente desde su base hasta el final. La carga elástica se calcula de forma que los esfuerzos transmitidos por los mecanismos de mando sean mínimos.
No obstante, a pesar de esta disposición de las espiras del muelle, en los motores rápidos (con régimen superior a las 2 500 RPM) se produce una serie de pequeñas oscilaciones debido a la propia velocidad de accionamiento que no dan tiempo al muelle a compensar por sí mismo sus propias oscilaciones ya que, antes de poder compensar la oscilación propia de la distorsión, debe entrar nuevamente en funcionamiento. Estas oscilaciones son independientes de la frecuencia propia de cada resorte, por lo que en estos casos hay que disponer un sistema que sea capaz de compensarlas, limitando la vibración al máximo.

Fig. N° 24. Comprobador de tensión de resortes
Con una máquina especial para comprobar la carga de los muelles, cuya deformación elástica debe corresponder a las características indicadas por el fabricante. Si no se dispone de esta máquina o no se conocen las características del fabricante, la comprobación se realiza por comparación con un muelle nuevo de las mismas características y destinado al mismo motor.
Se comprueba que las alturas en reposo de ambos muelles son iguales.
En caso de haber la menor variación en altura, indica que está deformado y entonces es conveniente sustituirlo por otro nuevo. El sistema actualmente empleado consiste en un doble muelle concéntrico con los arrollamientos de las espiras invertidos, con lo cual se consigue eficiencia mecánica, eliminando la posibilidad de que las espiras puedan entrelazarse y eficiencia dinámica, pues la oscilación propia de cada resorte es anulada por el otro, originándose un efecto de frenado por la acción de las fuerzas antagónicas de cada muelle.

Fig. N° 25. Componentes de resorte y válvula
- BLOQUE MOTOR.
El bloque motor constituye el cuerpo estructural donde se alojan y sujetan todos los demás componentes del motor, la forma y disposición del bloque está adaptada al tipo de motor correspondiente, según sea de cilindros en línea, horizontales opuestos o en V.
En la parte superior del bloque motor existen los huecos que forman los cilindros y hacen de recipiente para la mezcla del combustible; en estos huecos se forman la cámara de expansión de los gases quemados y además sirven de guía al émbolo durante su desplazamiento. En la parte inferior del bloque motor y sobre unas nervaduras de la bancada van situados los apoyos del cigüeñal.

Fig. N° 26. Componentes del motor
- REFRIGERACIÓN DEL BLOQUE MOTOR
- BLOQUE CON REFRIGERACIÓN POR AGUA
Los motores refrigerados por agua llevan situados en el interior del bloque unos huecos denominados "Camisas de Agua" en el argot popular también lo denominan "Chaquetas de Agua", a través de estos conductos que rodean a los cilindros circula el líquido refrigerante del sistema de refrigeración.

Interesante artículo! Gracias por la información que aporta!!
ResponderBorrar